The medical industry is one of the most demanding sectors when it comes to precision and reliability. From life-saving devices to diagnostic equipment, every component must meet stringent standards to ensure patient safety and optimal performance. At LEADMAKE, we understand these critical requirements and have been a trusted partner in the CNC machining of medical-grade metal and plastic components for years.
The Growing Need for Precision in Medical Manufacturing
In the medical field, the margin for error is virtually nonexistent. Whether it’s a surgical instrument, an implantable device, or a diagnostic machine, each part must be manufactured with the highest level of accuracy. This is where first-article inspection (FAI) and precision part machining play a pivotal role.
🔵First-Article Inspection (FAI):FAI is a critical step in the manufacturing process, ensuring that the first batch of parts produced meets all design specifications and quality standards. In the medical industry, this step is non-negotiable, as even the slightest deviation can lead to device failure or patient harm.
🔵Complex Part Manufacturing: Medical devices often require intricate designs with tight tolerances. CNC machining allows for the production of complex geometries in both metal and plastic, ensuring that each component performs its intended function flawlessly.
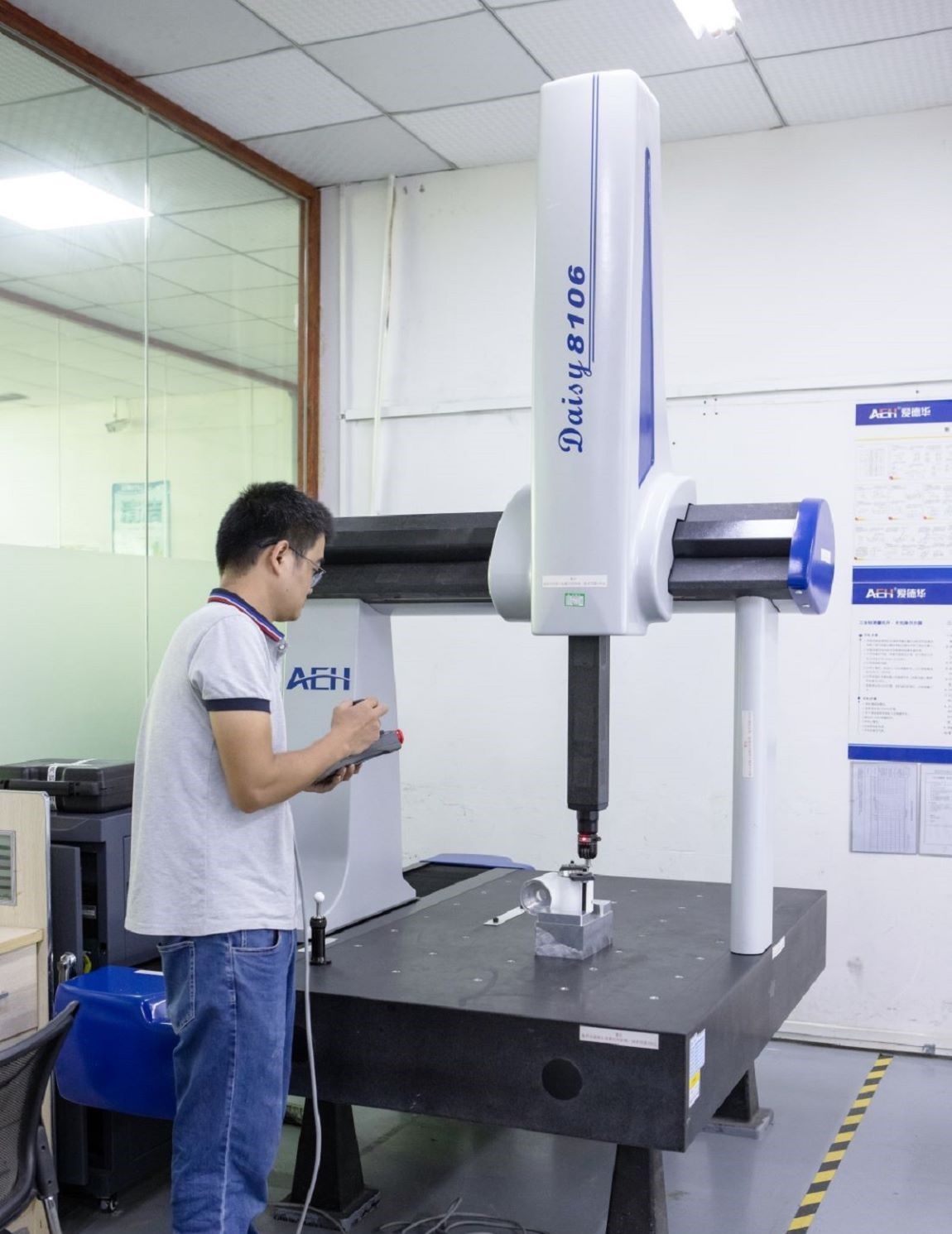
Our Expertise in Medical CNC Machining
At LEADMAKE, we specialize in the CNC machining of medical-grade materials, including stainless steel, titanium, aluminum, and high-performance plastics like PEEK. Our state-of-the-art facilities and experienced engineering team enable us to deliver components that meet the rigorous demands of the medical industry.
🔵Years of Experience: With over 18 years of experience in the field, we have honed our skills in producing high-precision parts for a wide range of medical applications. From surgical tools to imaging equipment, we’ve worked with leading medical device manufacturers to bring their innovations to life.
🔵Quality Assurance: We adhere to the highest quality standards, including ISO 13485 for medical devices. Our rigorous quality control processes ensure that every part we produce meets or exceeds industry requirements.
🔵Customer-Centric Approach:Our commitment to customer satisfaction is reflected in the positive feedback we receive from our clients. We work closely with our customers to understand their unique needs and deliver tailored solutions that exceed expectations.
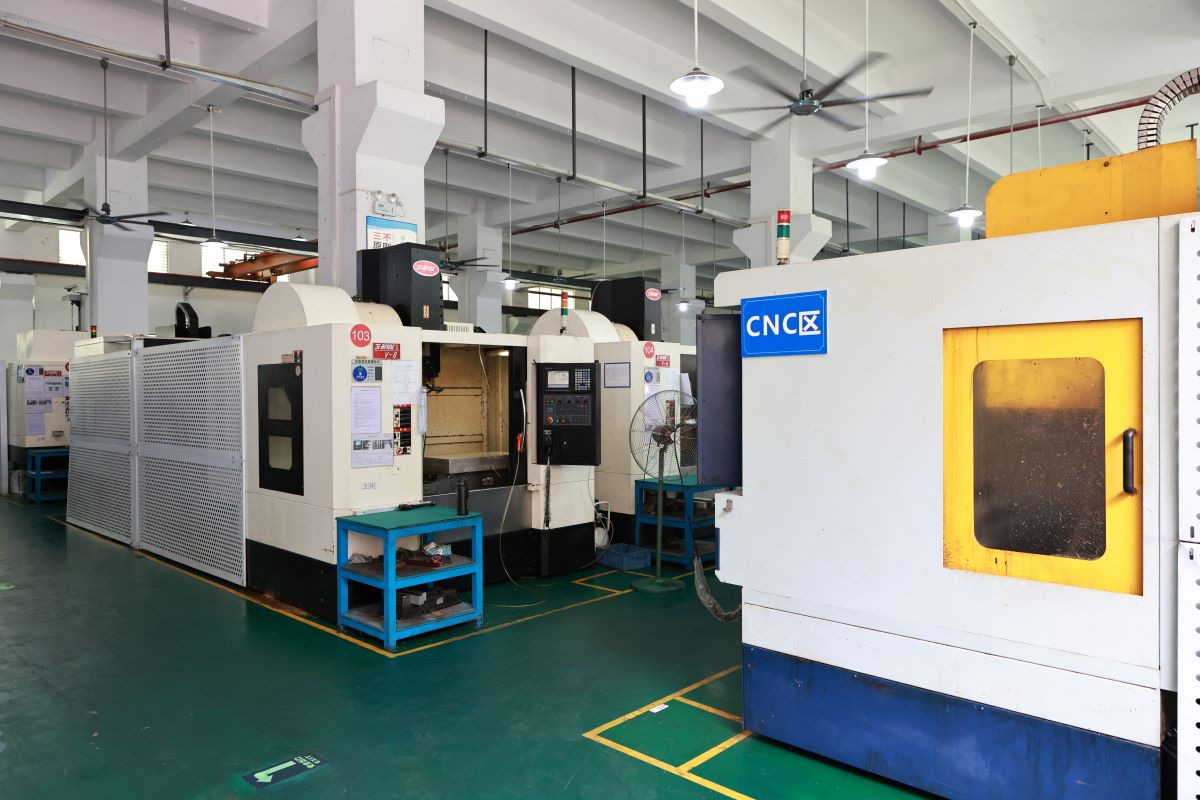
Why Choose LEADMAKE?
🔵Precision and Reliability: Our advanced CNC machining capabilities ensure that every component we produce is precise, reliable, and ready for use in critical medical applications.
🔵Quick Turnaround: We understand the urgency of medical projects and offer fast turnaround times without compromising on quality.
🔵Competitive Pricing: Our efficient manufacturing processes allow us to offer competitive pricing, making high-quality medical part machining accessible to businesses of all sizes.
Partner with Us for Your Medical Manufacturing Needs
The medical industry’s demand for precision and reliability is only growing, and at LEADMAKE, we are committed to meeting these needs with excellence. Whether you require first-article inspection, complex part machining, or ongoing production support, we have the expertise and resources to deliver.
Contact us today to learn more about how we can support your medical manufacturing projects and help you bring your innovations to market with confidence!